Realizując swój mały projekt po części przypadkowo trafiłem na szkolenie z druku 3D organizowane w naszym kole. Może „przypadek” nie jest do końca pasującym słowem, ale na pewno nie planowałem tam być, a tym bardziej jakoś szczególnie wciągać się w samo drukowanie.
Tak po prostu wyszło.
Szkolenie dotyczyło obsługi drukarek i ich działania, nieszczególnie zahaczało o projektowanie, choć w zasadzie myśląc o używaniu drukarki, to właśnie ono wydaje się największym wyzwaniem, prawda? Otóż nie do końca, ale może najpierw wyjaśnię trochę kontekst, żeby łatwiej wyobrazić sobie całą istotę problemu.
Potrzebowałem obudowy – w zasadzie mogłem się bez niej obejść, a cały projekt wcisnąć w puszkę po herbacie, ale nie bardzo uśmiechała mi się prymitywna walka z materiałem, mając do dyspozycji nóż i, w razie desperackiej potrzeby, widelec. Dodatkowo samodzielnie zaprojektowane części dodają całości pracy nieco smaku, windując motywację. Plan był prosty, zrobić jakąś kanciastą, względnie ładną strukturę, która będzie wystarczająco funkcjonalna, żeby ją wykorzystać.
Zanim dałem nura do poradników, zmierzyłem już kupione elementy i zrobiłem prosty rysunek w autocadzie (na tyle prosty, że prowadzący zajęcia złapaliby się za głowę – chciałem tylko zapamiętać wielkości otworów i odległości między nimi). Jako, że nie mam własnej drukarki próbowałem też myśleć o maksymalnym skróceniu czasu drukowania i minimalnym zużyciu filamentu.
Do projektowania znajomi polecili Fusion360, który możemy dostać za darmo jako studenci, program bardzo przejrzysty i niezbyt trudny do ogarnięcia, jeśli chcemy robić podstawowe projekty (zaawansowane może też, ale póki co nie wchodziłem głębiej). Na youtube roi się od poradników, które oczywiście nie zrobią za nas projektu, ale pokażą wszystko potrzebne do samodzielnej pracy i wcale nie potrzebujemy niezliczonych godzin, aby to ogarnąć.
Udało się finalnie całość skończyć i wydrukować, ale oczywiście nie obeszło się bez problemów, które spróbuję opisać, abyście mogli ich uniknąć, pokazując kolejne „skończone” prace.
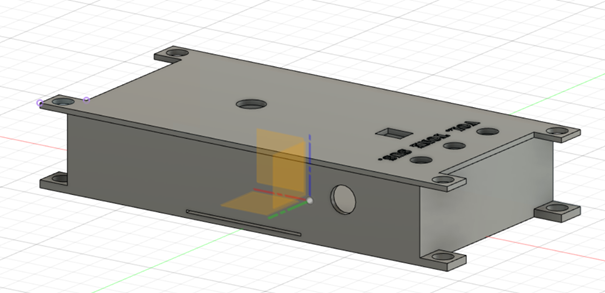
Chciałem mieć możliwość zamknięcia opakowania oraz uniknąć ogromnej ilości supportu (support to taka podbudówka z filamentu używana tylko do tego, żeby możliwe było wydrukowanie oczekiwanego elementu, później suport odrywamy i wyrzucamy). Jak można się domyślić, takie rozwiązanie średnio by wytrzymało, wyglądało i wymagało gigantycznych śrub, które dodatkowo ciężko by było zakręcić ze względu na okrągłe otwory i brak jakiegokolwiek wpustu.
Kolejnym problemem jest ten wąziutki, prostokątny otwór na dole opakowania, który miał być wykorzystany do ewentualnego uziemienia układu, jeśli byłaby taka potrzeba. Miał szerokość chyba dwóch milimetrów, a ze względu na swoją długość musiał być drukowany z supportem, całkiem możliwe, że w ogóle nie dałoby się tego suportu wyjąć po wydrukowaniu.
W tej wersji projektu jako ostatnia zawiniła moja potrzeba dopieszczenia całości, którą widać poniżej.
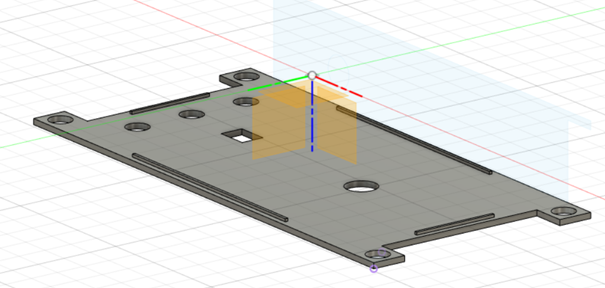
Mowa o wypustkach wychodzących z pokrywy, które same w sobie nie są złym pomysłem, ale oczywiście zależało mi na ładnym wyglądnie powierzchni obudowy. W tym przypadku, jeśli chciałbym te wypustki wykorzystać, element musiałby być drukowany w pozycji jak na obrazku, a to zniszczyłoby znacznie jakość napisów. Samo połączenie śrubowe wyrównuje ułożenie pokrywy, więc w tym przypadku chęci przerosły rzeczywiste potrzeby.
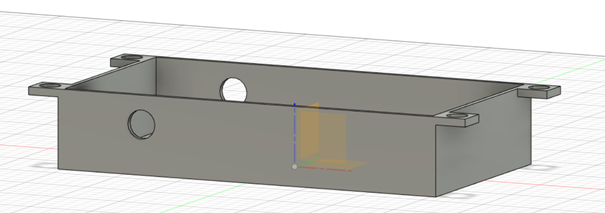
Kolejna zmiana, w zasadzie poprawna, bezpośrednie połączenie jest niezłe, jednak wymagałoby potężnej ilości suportu, czego raczej wolałem uniknąć. Dodatkowo same otwory są okrągłe, nakrętka nie ma się gdzie podziać i trzeba nieco się pobawić, żeby dobrze zamknąć lub otworzyć obudowę.
W ostatniej wersji pozbyłem się większości problemów i mówiąc o większości… pamiętajcie, żeby się upewnić, że każdy z otworów jest nieco większy od średnicy elementu, który chcecie przełożyć. Ja o tym zapomniałem w przypadku dwóch i miałem z tym trochę zabawy.
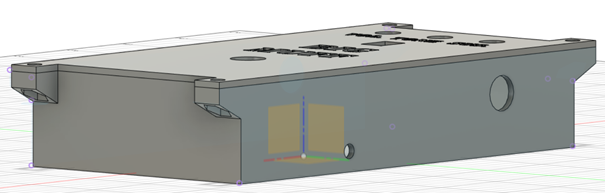
Wersja ostateczna zamiast długiego prostokąta zawiera otwór, przez który mogę przepuścić śrubę i od niej uziemić układ. Dodatkowo miejsce złączenia jest w pewnym miejscu ścięte, co ogranicza zużycie supportu, a jego wnętrze wygląda w ten sposób:
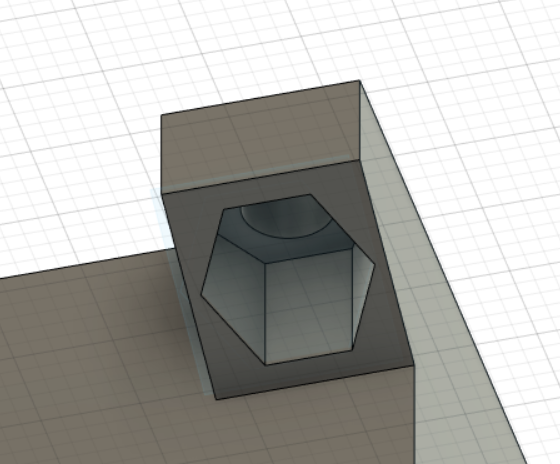
Przez okrągły otwór przechodzi śruba, natomiast do sześciokąta wchodzi nakrętka (wymiar okręgu wpisanego w projekcie jest większy o około milimetr od tego w nakrętce) i blokuję się tam podczas wkręcenia i wykręcania śruby, co okazuje się bardzo wygodne podczas otwierania lub zamykania pudełka.
I to w zasadzie tyle, błędy skorygować pomógł mi Kuba Wrona, a projekt wydrukował Grzegorz Radziwiłko, którym bardzo dziękuję za ogromną pomoc.
Tak wygląda cały, niemal skończony projekt:
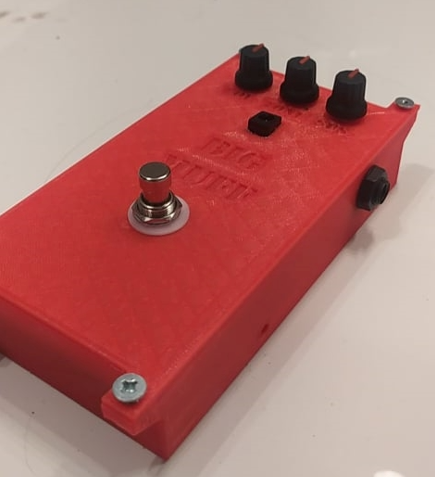
Uczyłem się od zera, więc okazuje się, że to naprawdę nie jest takie trudne. Zachęcam do spróbowania, bo to niesamowite uczucie trzymać wydruk swojego własnego projektu.
Marcin Ścibura
0 komentarzy